The aviation industry has long been at the forefront of technological advancements, with automation playing a crucial role in enhancing safety and performance. As an industry it can offer numerous lessons to other industries. These lessons come both in the form of drawing positive lessons how some automation has been integrated into the aviation industry in a positive manner, as well as taking heed of some warnings signs as automation has been adopted in a maladjusted way.
This page provides some examples of automation done right and instances where automation has led to unintended consequences, including incidents or accidents. It is important to understand technology or automation isn’t solely to blame here, but the full picture is always a more complex interplay of training, company policies, over-reliance on automation and many other factors.
For a more conceptual treatise on how and why the aviation industry is the #1 industry to draw lessons from when it comes to automation, read the Transition Level backstory.
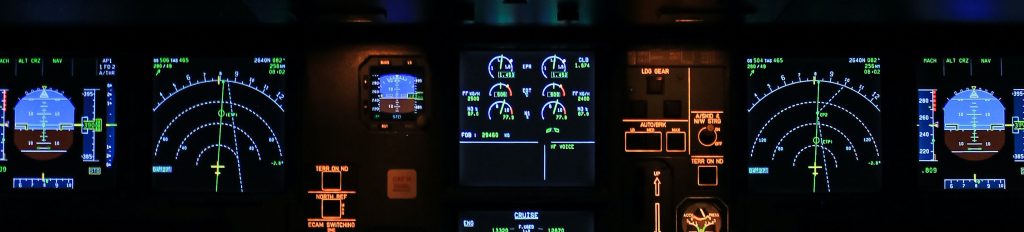
Automation done right: TCAS (Traffic Collision Avoidance System)
TCAS is designed to enhance safety by providing pilots with timely alerts and resolution advisories to prevent mid-air collisions between aircraft. This system demonstrates how automation, when thoughtfully implemented and integrated with human decision-making processes, can significantly improve safety and efficiency in aviation.
How TCAS Works:
TCAS is an airborne system that operates independently of ground-based air traffic control, continuously monitoring the airspace around the equipped aircraft for other aircraft equipped with a compatible transponder. Using interrogations and replies between the TCAS-equipped aircraft and other nearby aircraft, TCAS can determine the relative positions, altitudes, and trajectories of these aircraft.
When TCAS detects a potential conflict, it first issues a Traffic Advisory (TA), alerting the pilots to the presence of nearby aircraft that may pose a potential collision risk. If the threat of a collision increases, TCAS issues a Resolution Advisory (RA), providing the pilots with specific climb or descend instructions to avoid the conflicting aircraft. Pilots are trained to follow the RA promptly unless doing so would compromise safety (e.g., due to terrain or weather).
Mindful Automation Principles Demonstrated by TCAS:
- Collaboration, Inclusivity, and Global Perspective: TCAS is an internationally recognized and standardized system, developed and adopted through collaboration between aviation stakeholders, including aircraft manufacturers, airlines, and regulatory agencies. This collaborative approach has led to a more inclusive and universally effective solution for collision avoidance.
- Resilience and Adaptability: TCAS is designed to function independently of ground-based air traffic control systems, allowing it to provide collision avoidance support even in the absence of external inputs. This independence and adaptability make TCAS a resilient system in a complex and dynamic aviation environment.
- Transparency and Trust: TCAS has undergone extensive testing, evaluation, and refinement, ensuring its reliability and building trust among pilots and the aviation community. Pilots are trained to understand the system’s capabilities and limitations, fostering transparency and trust in the technology.
- Safety: TCAS directly addresses the critical aspect of aviation safety by reducing the risk of mid-air collisions by over 90%. The system has been proven to be highly effective, with numerous instances where TCAS RAs have successfully prevented potential collisions.
TCAS serves as an early example of mindful automation in the aviation industry.
Automation done right: HUD
A HUD enhances pilot situational awareness and reduces workload by projecting critical flight information directly into the pilots’ field of view, allowing them to maintain visual contact with the environment outside the cockpit. This innovation demonstrates how thoughtfully designed automation can improve the pilots’ flying skills, safety, efficiency, and the overall human-machine interaction in aviation.
How HUD Works:
A HUD is an advanced display system that projects essential flight information onto a transparent screen or surface, typically mounted just above the aircraft’s main instrument panel. This allows pilots to view critical data, such as airspeed, altitude, heading, and navigation information, without having to look down at the instrument panel. HUDs can also provide information not previously provided by any other instrument, such as the flight path vector. As a result, pilots can maintain continuous visual contact with the outside environment, reducing the need to shift focus between the instruments and the view outside the cockpit.
HUD technology is particularly beneficial during critical phases of flight, such as takeoff, approach, and landing, when pilots must maintain strict visual contact with the runway and surrounding environment. Importantly, in low-visibility conditions, using a HUD allows pilots to hand-fly landings that would have otherwise required the use of Autoland, a system that relegates the pilot to a pure systems monitor role when active. It therefore supports both maintaining and improving the pilots’ hand-flying skills.
Mindful Automation Principles Demonstrated by HUD:
- Human Wellbeing-Centric Design: HUD is designed to improve pilot situational awareness and reduce workload, enhancing overall safety and competence. By providing essential information directly in the pilots’ line of sight, HUD enables them to focus on critical tasks while maintaining visual contact with the environment. A HUD also allows for more hands-on flying in marginal conditions than previous solutions.
- Collaboration, Inclusivity, and Global Perspective: The development and implementation of HUD technology have involved close collaboration between various stakeholders, including aircraft manufacturers, airlines, pilots, and regulatory agencies. This inclusive approach ensures that HUD systems cater to the diverse needs of the aviation community, resulting in a more universally effective solution.
- Transparency and Trust: HUD systems have undergone extensive testing and evaluation to ensure their reliability and effectiveness, fostering trust among pilots and the aviation community. Additionally, HUD technology is designed to be intuitive and easy to understand, promoting transparency and adoption in its operation. Generally speaking, pilots love their HUDs.
- Safety: By enhancing pilot situational awareness and reducing workload, HUD technology directly contributes to aviation safety. Increased opportunity for manual flying also promotes maintenance and enhancement of core flying skills.
HUD technology in aviation serves as an excellent more recent example of mindful automation, demonstrating the potential benefits of integrating automation with human decision-making and focusing on safety, efficiency, and human wellbeing. By thoughtfully designing and implementing HUD systems, the aviation industry has successfully harnessed the power of automation to enhance pilot performance, safety, and situational awareness, setting a benchmark for other industries to follow in their pursuit of mindful automation.
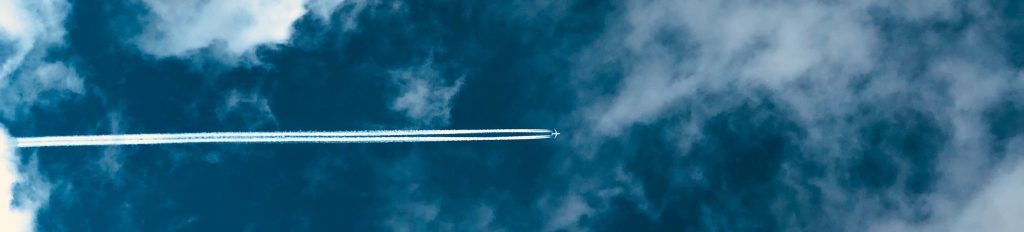
The aviation industry also, sadly, offers examples where automation has been implemented in a manner that has resulted in accidents.
Automation done wrong: MCAS (Maneuvering Characteristics Augmentation System)
The now-infamous MCAS system, resulting in two fatal crashes in 2018 and 2019, is a prime example of automation that very clearly was implemented in a flawed manner.
The Boeing 737 MAX aircraft featured a new software system called the Maneuvering Characteristics Augmentation System (MCAS). MCAS was designed to automatically adjust the aircraft’s nose down in certain flight conditions to prevent a stall. However, it relied on data from a single angle of attack (AoA) sensor. In both accidents, a malfunctioning AoA sensor caused the MCAS to activate inappropriately, repeatedly pushing the aircraft’s nose down. The pilots were unable to counteract the system and regain control, leading to the crashes.
Looking at MCAS from the perspective of Mindful Automation, there is a notable misalignment:
- Ethical Decision Making: The design of the MCAS system, particularly its reliance on a single AoA sensor, can be seen as an oversight in ethical decision-making.
- Human Wellbeing-Centric Design and Transparency and Trust: The pilots were not informed about the MCAS system, its operation, or how to disable it in case of a malfunction. The lack of transparency and training contributed to the pilots’ inability to handle the situation effectively.
- Safety: The MCAS system prioritized efficiency and cost over safety, as the design placed the aircraft at risk when relying on a single, potentially faulty sensor.
Automation done wrong: Air France Flight 447
The Airbus A330 aircraft was en route from Rio de Janeiro to Paris when it encountered severe weather. The pitot tubes, which measure airspeed, became obstructed by ice crystals, causing the airspeed data to become unreliable. The aircraft’s autopilot and auto-thrust systems disconnected as a result, transferring control back to the pilots. The pilots, likely confused by the situation and receiving conflicting information from the aircraft’s systems, made inappropriate control inputs, leading to a stall and the eventual crash.
Looking at the accident from the perspective of Mindful Automation, the misalignment includes:
- Human Wellbeing-Centric Design: The automation system did not provide adequate feedback to the pilots about the nature of the problem or the reason for the autopilot disconnection, contributing to confusion and inadequate response.
- Resilience and Adaptability: The system did not have a robust way of handling unreliable airspeed data and did not provide the pilots with clear guidance or an alternate mode of operation to manage the situation.
- Lifelong Learning and Skill Development: The pilots’ training may not have adequately prepared them to handle this specific emergency, emphasizing the need for continuous skill development and training (such as UPRT) in the face of increasing automation.